3D Printing Adds New Dimensions to Core Course on Soft Materials
McCormick students develop 3D printing materials in new hands-on labs
In the brightly lit MSE Teaching Laboratory inside Cook Hall, teams of Northwestern Engineering students peer into 3D printers, eagerly waiting to see their latest results. The materials they are printing parts with are not your standard resins. Each team has made their own resin formulation, developed over the quarter following insights they have collected over many printing and mechanical testing trials.
The results are clear on the students’ faces. Successful prints elicit smiles. Failed and unexpected ones prompt looks of focus and determination. They go back to work, tweaking their formulation to hopefully get the right outcome.
These moments are what Professor Ryan Truby envisioned when outlining the new 3D Printing Resin Design Labs for his course, MAT_SCI 331: Soft Materials.
A core undergraduate course in the Department of Materials Science and Engineering, Soft Materials now provides a hands-on approach to core learning outcomes that integrates fundamental principles with practical application. Soft Materials's Resin Design Labs challenge students to develop, refine, and optimize their own materials that culminate in 3D printing their own resins.
Truby said his early teaching experiences influenced his goal of developing the labs. He recalled that when he was a graduate student at Harvard University, he and his PhD adviser developed hands-on materials science activities for her biomaterials class, and the students’ engagement made a lasting impression.
"Those first teaching experiences and my research in 3D printing inspired the idea of having students develop their own 3D printing resins as a materials engineering project,” said Truby, June and Donald Brewer Junior Professor and assistant professor of materials science and engineering and of mechanical engineering.
Truby first outlined the concepts behind the new labs in his faculty application to Northwestern, describing his vision for a course where students would design, characterize, evaluate, and 3D print their own materials. The redesigned class was supported by Truby’s 2023-24 Searle Fellowship with Northwestern’s Searle Center for Advancing Learning and Teaching and a 2023 Murphy Society Award he received with Professor Jonathan Emery, associate professor of instruction in materials science and engineering.
Now equipped with a dozen desktop resin 3D printers available for small student teams, the course is designed to integrate a range of interdisciplinary materials science topics such as polymerization reactions and the structure-property relationships of polymers.
“3D printing as a technology requires interdisciplinary materials science and engineering knowledge, spanning organic chemistry and polymer physics to rheology and mechanics," Truby said.
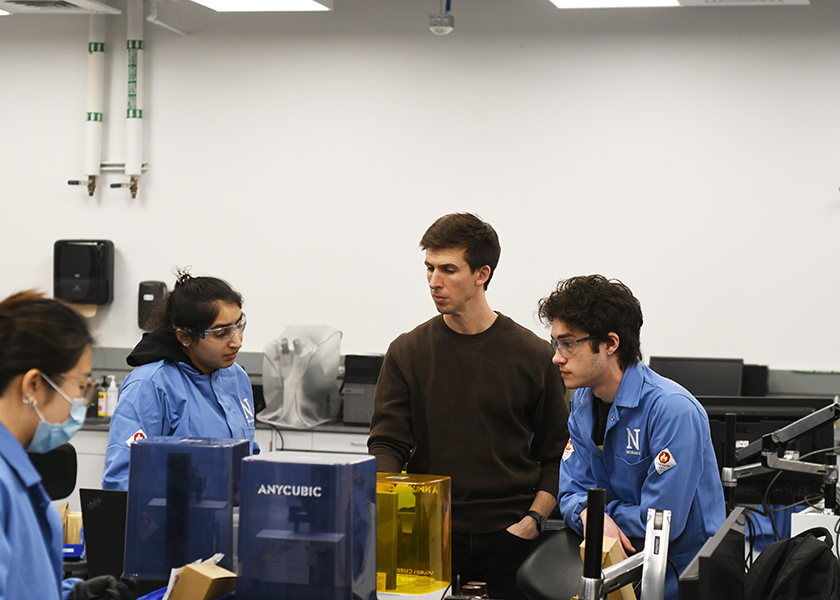
From concept to creation
During the course, which recently concluded its winter quarter section, students work in teams to create 3D-printing resins used to produce a functioning plastic buckle capable of withstanding heavy loads. The students progress through six intensive labs, gaining experience in 3D printing, materials characterization, and mechanical testing. The iterative process challenges them to translate theoretical knowledge into functional materials while troubleshooting issues along the way.
“One of the most exciting parts of science is working hands-on. It helps bring science to life – particularly in materials science where intuition and knowledge can be built through the tactile experience of simply manipulating different materials,” said teaching assistant Emmy Markgraf, a PhD student in Truby’s Robotic Matter Lab. “Having the students experience how changing their resin formulations can lead to stronger or weaker 3D-printed parts not only challenges their problem-solving skills but also bridges that connection from what they learned in lectures.”
"The class greatly surpassed my expectations, offering far more hands-on experience than anticipated,” third-year undergraduate Julia Wiater said. “The lab challenge that structured the entire course was particularly engaging and provided a stimulating learning environment."
Hayden Williams, another third-year student in the course, appreciated the freedom students were given to explore different approaches.
"I really loved this class. Working with resin 3D printers was a new experience that was really fun. I felt I had a large amount of control, which was nice as most other lab-based courses focus on one very specific test or experiment,” Williams said. “In this course, we were given a specific end goal but had an immense amount of freedom for how to get there."
The hands-on structure of the course requires students to grapple with real-world engineering challenges. Truby noted that one of the biggest hurdles is designing a new resin from scratch. Students must rapidly screen blends of available reagents to determine which combinations will yield functional resins that properly 3D print desired parts.
Students must also analyze mechanical characterization data as part of this screening process to optimize their resin formulations, a process that demands both critical thinking and problem-solving skills.
"Successful teams also collaborate, learn from other teams, and reflect on their data as they rationalize steps in their design process," Truby said.
The collaborative nature of the course encourages students to learn from both successes and failures. The ability to iterate and refine designs is a key component of the learning experience, reinforcing important engineering concepts in a tangible way.
Teaching assistants such as Alex Evenchik also play a crucial role in guiding students through the process, providing a helping hand when needed but still empowering students to find their own way.
“It has been incredibly rewarding to see the growth of the students, going from not knowing what a polymer is to designing resin formulations that you cannot purchase or have never been made before,” said Evenchik, a PhD candidate in Truby’s lab.
A new model for materials science education
Truby emphasized that hands-on learning builds connections between fundamental and emerging engineering concepts. The course’s 3D Printing Resin Design Labs have established a model for integrating engineering fundamentals with practical applications. By working through complex design challenges, students not only build a deeper understanding of materials science but also gain confidence in their ability to engineer materials for real-world applications.
"In all my courses, I strive to create learning opportunities that enable students to form connections between established engineering fundamentals and emerging ones critical to becoming a modern engineer,” he said. “I also encourage students to see both success and failure as essential to the learning process. Traditional coursework does not empower students to learn from failures like hands-on projects do."
Wiater reflected on how the class shaped her problem-solving skills while working with classmates.
"This class encouraged me to advance my problem-solving approach, strengthened my critical decision-making skills, and prepared me to effectively communicate my ideas to a broader audience,” Wiater said.
Tasked with developing long-form labs, Evenchik found the teaching experience to be just as valuable as the learning experience was for students.
"The lessons I learned are skills I will carry with me into my future career,” he said.
Northwestern Materials Science: Historic Leadership, Innovative Learning, Interdisciplinary Research
Established more than 60 years ago as the first materials science academic department in the world, Northwestern Engineering’s Department of Materials Science and Engineering remains at the forefront of the field. Our research is centered around four areas that are critical for society: energy materials, sustainability materials, medical materials, and AI for materials discovery and characterization. We pursue this research through deep interdisciplinary partnerships across Northwestern University, with national labs, museums, and other external partners. This creates and ideal environment not only for researchers, but also for students as it exposes them to a wide variety of facilities, internship and networking opportunities, and an entrepreneurial environment that introduces them to research translation.